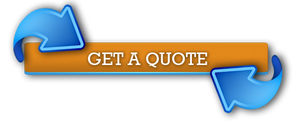
Powder Coatings
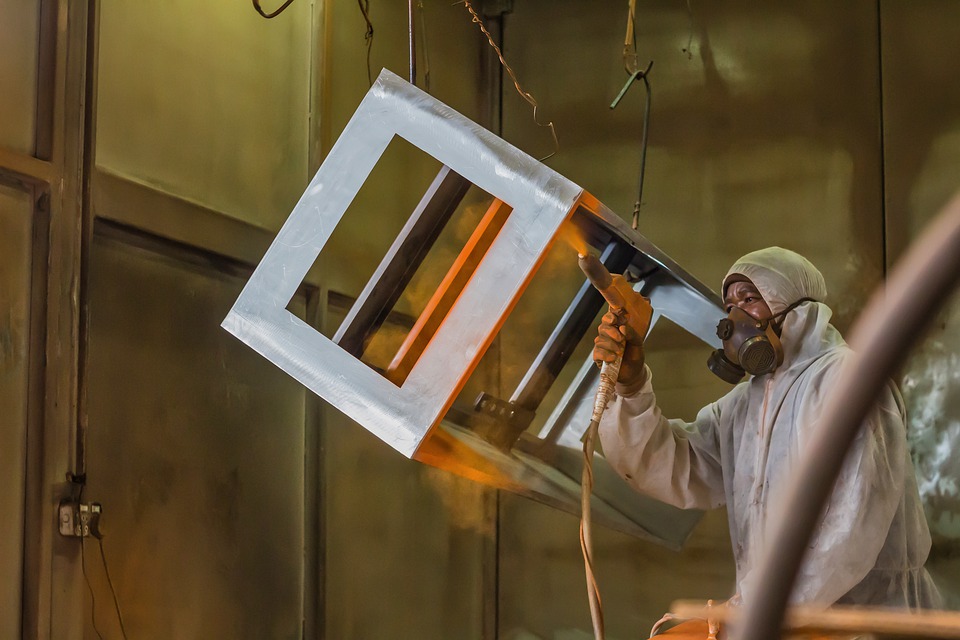
Powder coating has been generally regarded as an environmentally friendly method of applying the finish. This is because it avoids overspray wastage, the use of solvent-based paints, and any powder that is unused can be recycled and reused.
Although these powder coating methods were regarded to be a method of metal finishing, advancements in technology have made it a common choice for wood, plastics, and even ceramics. According to research, this powder coating is among the fast-growing coating medium due to its excellent finishing properties coupled with environmental advantages. This is one trend that is likely to continue even with time.
Types of powder coating
We have two main types of powder coatings; the thermoplastics and the thermosets. with the thermoset’s variations, when the powder bakes, it will react with the other chemicals in the powder polymer which will help in the increase of the molecular weights and also improvement of the performance properties.
Thermoplastics on the other hand do not change and neither do they have any additional reactions. This simply flows out into the final coatings.
Powder coating process
This mainly deals with the preparation of the part or component. And just as any other paint application, preparation is all necessary so as to be able to achieve the best possible finish. During this phase, it is essentially removing all the metal oxides, lubricants, and oils. This is usually done by the use of some mechanical and chemical processes depending on the finish required, its size, and the material. The multiple stage chemical pre-treatment entails using the chromates and phosphates by spraying or submersion. However, from the environmental view, the most ideal component during the preparation process is the phosphate as the chromates could be environment toxic. Another method that can be used in the preparation is the shot blasting and sandblasting. This is where the blasting abrasives are used in giving the surface texture and the preparation of glass, plastic, and wood. Silicon carbide is the most appropriate when it comes to metal grinding. The plastic media blasting however uses the plastic abrasives that are usually that sensitive to the substrates like aluminum. The most common method used in the powder coating application is electrostatic spraying through a spray gun. In this case, the objects get grounded and the gun imparts positive electric charges onto the powder. This is then accelerated and sprayed towards the components using the power of the electrostatic charges. The component is then later heated and the powder melts into a uniform film that cools forming the hard coatings. However, sometimes the metal is heated first and then the powder sprayed onto the hot substrate. These pre-heating techniques can aid in the achievement of more uniform finishes. However, this can have other problems such as runs due to excessive powder. More so, the powder can be applied using the precisely adapted electrostatic discs. Another method is the Electrostatic Fluidised Bed Coating. This is whereby the electrostatic charging will occur in the bed so that the powder becomes charged while the fluidizing air is lifting it up. The powder particles that are charged then form a cloud of powder above the fluid beds. When thus a grounded part passes through the charged cloud, these particles get attracted to these surfaces. Typically, these parts are not always preheated. Lastly, we have the Electrostatic Magnetic Brush (EMB) coating. This coating is mainly used for the flat materials and regularly applies the powder coating using the roller technique. When the thermosets powders get exposed to the high temperatures, they start melting, flowing out, and reacting forming higher molecular weight polymers. This curing process known as the cross-linking will thus need a certain temperature degree for a certain duration for it to get full cure thus establishing the full film properties that the materials were designed. Pre treatment
The powder application
Curing
The advantages of Powder Coating
- Resilient to most chemicals and solvents
- Cost-effective
- Rust free
- Excellent electrical insulation capabilities
- Immense range of colors and finishes
- Environmentally friendly as there are no solvents required
- Fast turnaround times
- Finishes are strong and supple making it rigid to damage or crack
- Almost no waste production
- Application can be done on a wide range of thickness
- it gives a hundred percent solid coating
- Excellent color retention
- it gives easy accomplishment of the special effects
- produces thick coatings without sagging or running
- Safeguard against exterior UV fading
The disadvantages of Powder Coating
- The color uniformity and matching could be harder compared to liquid paints
- Maintaining the thickness uniformity needs expertise
- Can be that tricky on the sharp corners
- The frequent color changes could be that time consuming
- The thin coatings could show pinholes
Metallic Powder Coating Process-Problem & Solution
The metallic powder coatings are usually the decorative protective finishes applied to metals for finishing applications. These multi-colored metallic powders are mainly applied using a single application and later coated with the clear powder for the more enhancement of the finish. The mica and metallic powder coatings mainly contain the mica or metal flake that help in the giving of these coatings that special appearance. Typically, these particulars and flakes are always freestanding components. These powder coatings are evenly blended with base color powders. This is referred to as the Dry Blended Powders and is available in TGIC Polyester chemistries, Urethane, Hybrid, and Epoxy.
However, the main problems with these dry-blended powders are limited ability to be recycled, limited penetration in recessed areas, and color consistency. These dry blended powders are applied by the use of the corona gun that has a flat spray nozzle. The mica and metallic powder coatings are processed by the physical bonding to the surfaces of the powered coatings. In general, all the mica and metallic particles are usually bonded however, we have some that will not firmly attach and thus causing problems during the finishing process.
The bonded mica and metallic powders have fewer lines than the dry blended powders and thus are recyclable. Additionally, they provide a consistent colour after the recycling process and have less picture frame effect. More so, they have higher transfer efficiency and better penetration. However, though this bonded metallic and mica powders can be retrieved, it is best minimizing the ratio of these powder to virgin powder to ensure the production of the best possible finish.
The metallic powders have some disadvantages associated with them. The first is that aluminized powder finishes tend to look worn with time. Also, another drawback is loading one of the most uncontrollable loss of electrostatic high voltage power. However, to reduce this loading a designed spray muzzle can be put under use where the amount of metal in the powder is not that excess. This powder also has been a major cause of the several spray booths fires.
Spice powder coatings are the exceptional blends of the various finished powder colours that result in the highly protective and aesthetic coatings. These multi-coloured powders are always available in Urethane, Hybrid, Epoxy and TGIC Polyester chemistries. This kind of powder coatings are mainly used for the end-use applications such as leisure equipment, case goods, shelving and casual furniture.
Spice powder coatings have no challenges compared to the use of the solid color and smooth powders. What the applicators need doing is applying consistent color patterns to some film thickness consistency producing quality appearances. Due to the nature of these spice powder coatings, the appearances and color of the coatings may vary when the powder is recycled.
Powder coatings are an economical system that not only completes desired aesthetic qualities but also offers excellent resistance to chemical corrosion, scratches and offers the durability of the product even in the harsher environments. Therefore, all you need is working with the best companies to get the best-desired results. Always find the right experts like Contract Manufacturing Specialists of Michigan for the best superior film properties.
Given the quality of staff and equipment that we have, you can be sure of getting the best rates from our brand. To benefit from our services, feel free to call us today. We have a team that is ready to give you the best services all the time.
Our core offerings and services at Contract Manufacturing Specialists of Michigan includes, but is not limited to, the following below:
We service multiple cities throughout the state of Michigan. We provide all the services listed above, and much more in every city throughout Michigan.
If you don’t see your city listed or a specific service listed, don’t worry. All you have to do is contact us by either giving us a call or filling out our online contact form. Then we’ll discover what are some of the top solutions for you, your business, and executing a solid solution.